Non-Metallic Materials
Don’t see what you need? New Process Fibre is a one-stop shop manufacturer who can execute any non-metallic custom orders you provide that are not listed within the product catalog.

Fabrication Services
New Process Fibre has been stamping and die cutting non-metallic washers, spacers, gaskets, shims, and many other custom shapes for a variety of customers since 1927.At our 55,000 square foot facility, we provide quality and service to our customers that add value and provide a competitive advantage to their projects in the aerospace/military, construction, industrial, archery, automotive, electronic, fastener, furniture, hunting, fishing, elevator, power hand tool, plumbing, marine, transformer and numerous other industries.
We offer a wide array of colors, including red, green, blue, yellow, black, orange and white; color matching is also available on certain materials. (Minimum quantities may apply for special colors.)
New Process Fibre offers:
- Sheet extrusion and slitting
- Slitting and shearing
- In-house tool and die making
- Non-metallic stamping
- Embossing/screen printing/nomenclature on custom parts
- Pressure Sensitive Adhesive (PSA) applied to stamped parts
- Materials and stamped parts in either English and/or metric units
Select from the Fabrication Services options below to learn more about New Process Fibre's fabrication offerings.

Custom Washers
New Process Fibre, an ISO 9001:2015 non-metallic stamping company, manufactures flat and specialty washers for the fastener industry using a large variety of materials such as Nylon, Nylon 6, Nylon 6/6, High and Low Density Polyethylene, Polypropylene, PEEK®, Flame Retardant Polypropylene, Acetal, ABS, Mylar®, Teflon™ PTFE, Vulcanized Fibre, Fish Paper, Nomex®, Viton®, Paper Phenolic, PVC, Polycarbonate, Ultem®, Buckfab, and Epoxy Glass.With over 10,000 washer dies in stock, we can meet your requirements in as little as 1 week - or less! We fabricate washers with outside diameters from 0.093" to a maximum of 12.000", thicknesses from 0.005" to 0.187", and quantities ranging from just 1 into the millions per order.
Our team has years of experience working a broad range of materials, building their own die-sets in-house, and stamping washers to exact tolerances with an extremely fast turnaround, regardless of order quantity.
We offer a large array of colors, including red, green, blue, yellow, black, orange and white, and provide color matching on certain material options. (Minimum quantities may apply for these special colors.)
All custom washers available in English and/or metric units and can have Pressure Sensitive Adhesive (PSA) applied.
Select from the Custom Washer options below to learn more about New Process Fibre's specially tailored washer offerings:
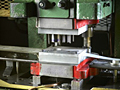
Stamped Parts
With more than 10,000 washer dies in-house and 75 conventional and high-speed punch presses intended to punch both strip and coil stock, New Process Fibre is well-equipped to handle standard and custom part orders of any size. Ready to handle requests ranging from a single part to multi-millions, our team is experienced in production with a broad variety of materials.We have a wide selection of materials in stock, including Acetal, Buckfab, Delrin®, Epoxy Glass, Fish Paper, Mylar®, Nomex®, Nylatron®, Nylon MDS, Nylon 6 and Nylon 6/6, Phenolic, Polyethylene, Polypropylene, Teflon™ PTFE, PEEK®, PVC, UHMW, Ultem®, Vulcanized Fibre, and much more.
New Process Fibre can form custom washers, spacers, tags, end laminations, gaskets, insulators, and many other specialized parts in an array of color options.
- CAD files accepted
- Short and High Run Stampings
- In-house prototype runs using steel rule dies for die cutting
- Progressive Stampings
- Custom Die creations
- Special shapes, such as diamond, oval, triangle, rectangle, round, and many more
- Critical tolerances achieved, specifically for thicknesses from 0.005" to 0.250" and formed parts as small as 0.093" in diameter to as large as 24" square
- Embossing/screen printing/nomenclature on custom parts
- PPAP (Product Part Approval Process) available
- Pressure Sensitive Adhesive (PSA) applied to stamped parts
Select from the Stamped Part options below to learn more about New Process Fibre's specific stamped part offerings:
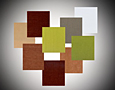
Stamping Materials
New Process Fibre stamps a vast array of non-metallic materials ranging from pressboard, vulcanized fibre, and fish paper to engineered thermoplastics such as HDPE, LDPE, Acetal, Nylon 6, 6/6, MDS, Polypropylene, and NEMA grade industrial laminates from XP, XXX Phenolic resins, glass epoxy based materials like G-3, FR-4, G-10 and GPO 1, 2, & 3 and other performance materials such as Mylar®, Nomex® and Teflon™ PTFE to meet your critical design criteria.We offer a wide variety of colors, such as white, red, orange, yellow, green, blue, and black; color matching is also available for some materials. (Minimum quantities may apply for special colors.) All stamping materials are available in English and metric units.
Select from the Stamping Material options below to learn more about New Process Fibre's vast material offerings:

Plastic Sheets & Rolls
There are two good reasons New Process Fibre maintains an extensive capability in thermoplastics extrusion. The first is to assure an unlimited supply of top quality materials for our non-metallic stamped products. The second is to make sure we can provide this same assurance to customers who want top quality thermoplastic sheet stock, strips, and continuous rolls and coils.All sheets, rolls, and coils are available in English and/or metric units and in a variety of standard and custom color options.
At New Process Fibre, we offer:
- A wide range of extruded thermoplastic sheet options
- UV Stabilizers
- High Density and Low Density Polyethylene, (HDPE & LDPE)
- Standard and Flame Retardant Polypropylene, Nylon 6 & 6/6, MDS and Filled Nylon, Acetal Copolymer and Homopolymer
- Thicknesses from 0.005" to 0.250"
- Material tolerances as quoted or to customer specifications
- Widths from 0.5" to 38" untrimmed
- Affordability in small quantities, with special discounts for higher volumes
Select from the Plastic Sheets & Rolls options below to learn more about New Process Fibre's specific stamped part offerings: