Non-Metallic Materials
Don’t see what you need? New Process Fibre is a one-stop shop manufacturer who can execute any non-metallic custom orders you provide that are not listed within the product catalog.

Custom Washers
New Process Fibre, an ISO 9001:2015 non-metallic stamping company, manufactures flat and specialty washers for the fastener industry using a large variety of materials such as Nylon, Nylon 6, Nylon 6/6, High and Low Density Polyethylene, Polypropylene, PEEK®, Flame Retardant Polypropylene, Acetal, ABS, Mylar®, Teflon™ PTFE, Vulcanized Fibre, Fish Paper, Nomex®, Viton®, Paper Phenolic, PVC, Polycarbonate, Ultem®, Buckfab, and Epoxy Glass.With over 10,000 washer dies in stock, we can meet your requirements in as little as 1 week - or less! We fabricate washers with outside diameters from 0.093" to a maximum of 12.000", thicknesses from 0.005" to 0.187", and quantities ranging from just 1 into the millions per order.
Our team has years of experience working a broad range of materials, building their own die-sets in-house, and stamping washers to exact tolerances with an extremely fast turnaround, regardless of order quantity.
We offer a large array of colors, including red, green, blue, yellow, black, orange and white, and provide color matching on certain material options. (Minimum quantities may apply for these special colors.)
All custom washers available in English and/or metric units and can have Pressure Sensitive Adhesive (PSA) applied.
Select from the Custom Washer options below to learn more about New Process Fibre's specially tailored washer offerings:
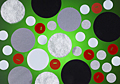
Custom Discs
(4)New Process Fibre is an ISO 9001:2015 Non-Metallic stamping company fabricating Discs from a large array of materials such as; ABS, Felt, Nylon, Nylon 6, Nylon 6/6, Acetal, Polypropylene, Flame Retardant Polypropylene, Polyethylene, Klinger®, Delrin®, Mylar®, PEEK®, Teflon™ PTFE, PVC, Ultem®, Vulcanized Fibre, Fish Paper, Nomex® and Viton®, into various custom disc shapes.
Tooling Available - If a Partial Tooling Charge occurs for all Hard Tooling it is a onetime charge. Tooling remains the property of New Process Fibre Company. New Process Fibre is responsible for the Maintenance and/or Replacement of the tool due to wear and tear, not dimensional changes, for the life of the part.
A large array of colors and/or color matching is available on certain materials. Standard colors available are Red, Green, Blue, Yellow, Black, Orange and White. Minimum quantities may apply for special colors.
All Custom Discs are available in English and/or Metric Units.
- Filter applications
- Restaurant Table Leg Anti Wobble Shim applications
- Spacer applications
- Ware resistance components
To learn more about Custom Discs and obtain a free sample or request a formal quotation, please complete our on-line form by clicking the "REQUEST INFORMATION” tab above.
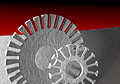
Custom End Laminations
New Process Fibre is an ISO 9001:2015 Non-Metallic stamping company fabricating End Laminations from materials such as; Vulcanized Fibre, Fishpaper and Nomex® into custom designs to fit your motor application needs.
Tooling Available - If a Partial Tooling Charge occurs for all Hard Tooling it is a onetime charge. Tooling remains the property of New Process Fibre Company. New Process Fibre is responsible for the Maintenance and/or Replacement of the tool due to wear and tear, not dimensional changes, for the life of the part.
Standard colors available in Red, Grey, White and Black Vulcanized Fibre.
All Custom End-Laminations are available in English and/or Metric Units.
- Motor components using End Laminations in Stators, Armatures and Rotors
- Household Kitchen Appliances
- Air purifier applications
- Uses found in Vacuum Cleaner Canisters
To learn more about Custom End Laminations and obtain a free sample or request a formal quotation, please complete our on-line form by clicking the "REQUEST INFORMATION” tab above.

Custom Gaskets
(16)New Process Fibre is an ISO 9001:2015 Non-Metallic stamping company fabricating Gaskets from a large variety of materials such as Mylar®,Teflon™ PTFE, Vellumoid®, Vulcanized Fibre, Fishpaper, Kapton®, Klinger®, Nomex®, Cork, Felt, Epoxy Glass, Paper Phenolic, Vegetable Fibre, Viton®, Garlock® and Thermoseal®, Silicone rubber, Acetal, Polypropylene, PVC, Nylon, Nylon 6, Nylon 6/6, Nylon MDS, High Density Polyeythlene and Low Density Polyethylene.
Tooling Available - If a Partial Tooling Charge occurs for all Hard Tooling it is a onetime charge. Tooling remains the property of New Process Fibre Company. New Process Fibre is responsible for the Maintenance and/or Replacement of the tool due to wear and tear, not dimensional changes, for the life of the part.
A large array of colors and/or color matching is available on certain materials. Standard colors available are Red, Green, Blue, Yellow, Black, Orange and White. Minimum quantities may apply for special colors.
All Custom Gaskets are available in English and/or Metric Units.
- Many material types are available for:
- Plastic Gaskets
- Fibre Gaskets
- Epoxy Gaskets
- Phenolic Gaskets
- Gasoline Motor Exhaust, Oil Field, Electronic Power Tool applications
- High degree of repeatability, precision and cost effective designs are standard
To learn more about Custom Gaskets and obtain a free sample or request a formal quotation, please complete our on-line form by clicking the "REQUEST INFORMATION” tab above.
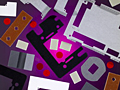
Custom Insulators
(16)New Process Fibre is an ISO 9001:2015 Non-Metallic stamping company fabricating Insulators from a large list of materials such as; X, XP, XPC, XX, XXP, XXX, Canvas Phenolic, Linen Phenolic, Mylar®, Teflon™ PTFE and Glass Filled Teflon™ PTFE, Glass Polyester, GPO-1, GPO-2, GPO-3, Vellumoid®, Vulcanized Fibre, Fishpaper, Kapton®, Klinger®, Nomex®, Duroid®, Epoxy Glass, G-5, G-7, G-9, G-10, FR-4 and G-11, Viton®, Lexan®, Garlock®, Acetal, Polypropylene, Nylon, Nylon 6, Nylon 6/6, Nylon MDS, High Density Polyeythlene and Low Density Polyethylene.
Tooling Available - If a Partial Tooling Charge occurs for all Hard Tooling it is a onetime charge. Tooling remains the property of New Process Fibre Company. New Process Fibre is responsible for the Maintenance and/or Replacement of the tool due to wear and tear, not dimensional changes, for the life of the part.
A large array of colors and/or color matching is available on certain materials. Standard colors available are Red, Green, Blue, Yellow, Black, Orange and White. Minimum quantities may apply for special colors.
All Custom Insulators are available in English and/or Metric Units.
- Electrical Insulation Components
- Transformer applications
To learn more about Custom Insulators and obtain a free sample or request a formal quotation, please complete our on-line form by clicking the "REQUEST INFORMATION” tab above.
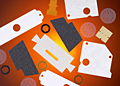
Custom Parts
New Process Fibre is an ISO 9001:2015 Non-Metallic stamping company fabricating custom Parts or Shapes from a large variety of materials such as; Mylar®, PVC, Teflon™ PTFE, Glass Filled Teflon™ PTFE, Vellumoid®, Vulcanized Fibre, Fishpaper, Kapton®, Klinger®, Nomex®, Cork, Felt, Epoxy Glass, Viton®, Garlock®, PEEK®, Thermoseal®, ABS, Acetal, Polypropylene, Nylon, Nylon 6, Nylon 6/6, Nylon MDS, Ultem®, High Density Polyeythlene and Low Density Polyethylene into a custom component shapes.
Tooling Available - If a Partial Tooling Charge occurs for all Hard Tooling it is a onetime charge. Tooling remains the property of New Process Fibre Company. New Process Fibre is responsible for the Maintenance and/or Replacement of the tool due to wear and tear, not dimensional changes, for the life of the part.
A large array of colors and/or color matching is available on certain materials. Standard colors available are Red, Green, Blue, Yellow, Black, Orange and White. Minimum quantities may apply for special colors.
All Custom Parts are available in English and/or Metric Units.
- Cup, C-shape, D-shape, Hex, split, slotted, slit, rectangular, square washers
- Military Fasteners
- Guitar Bobbins
- Plastic Balloon Ties
- Pressure Sensitive Adhesive applications
- Buna-Rubber Phenolic composites stampings
- Sanded parts to close tolerances
- Component applications for the Automotive, Electronic, Furniture, Marine and Plumbing industries
To learn more about Custom Parts and obtain a free sample or request a formal quotation, please complete our on-line form by clicking the "REQUEST INFORMATION” tab above.
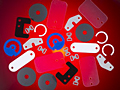
Custom Spacers
(23)New Process Fibre is an ISO 9001:2015 Non-Metallic stamping company fabricating standard and custom Spacers from a large variety of materials such as; Acetal, Polypropylene, Nylon, Nylon 6, Nylon 6/6, Nylon MDS, High Density Polyeythlene, Low Density Polyethylene, Canvas Phenolic, Linen Phenolic, Phenolic, Epoxy Glass, Mylar®, PEEK®, Teflon™ PTFE, Ultem®, Vulcanized Fibre, Fishpaper, Nomex®, PVC, and ABS into various Spacer shapes and sizes.
Tooling Available - If a Partial Tooling Charge occurs for all Hard Tooling it is a onetime charge. Tooling remains the property of New Process Fibre Company. New Process Fibre is responsible for the Maintenance and/or Replacement of the tool due to wear and tear, not dimensional changes, for the life of the part.
A large array of colors and/or color matching is available on certain materials. Standard colors available are Red, Green, Blue, Yellow, Black, Orange and White. Minimum quantities may apply for special colors.
All Custom Spacers are available in English and/or Metric Units.
- Hex, Half Hex, and Center Spring Spacers are available
- Cheaper and Non-corrosive compared to metallic Spacers
- Safety Helmet Components
- Slotted and Perforated Spacers
- Seat Belt Retainers
- Washing Machine Hose Brackets
- Refrigerator Door Spacers
- Aerospace Components
- Military Personnel Components
To learn more about Custom Spacers and obtain a free sample or request a formal quotation, please complete our on-line form by clicking the "REQUEST INFORMATION” tab above.
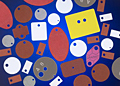
Custom Tags
New Process Fibre is an ISO 9001:2015 Non-Metallic stamping company fabrication of Custom Plastic Tags and Custom Non-Plastic Tags made from a large variety of materials such as; ABS, High Density and Low Density Polyethylene, Vinyl, PVC, Polypropylene, PEEK®, Acetyl, Nylon, Nylon 6, Nylon 6/6, Ultem®, Vulcanized Fibre and Epoxy Glass. Custom designed tags will give your product a professional finished look.
Tooling Available - If a Partial Tooling Charge occurs for all Hard Tooling it is a onetime charge. Tooling remains the property of New Process Fibre Company. New Process Fibre is responsible for the Maintenance and/or Replacement of the tool due to wear and tear, not dimensional changes, for the life of the part.
A large array of colors and/or color matching is available on certain materials. Standard colors available are Red, Green, Blue, Yellow, Black, Orange and White. Minimum quantities may apply for special colors.
All Custom Tags are available in English and/or Metric Units.
- Available as Blanks or with Names and Nomenclature Stampings on Tags
- Hang Tabs: Euro, J-Hook, Round, Rectangle, Square and Trianagle Tags
- Write on and Lock-out Tags in various colors
- Key Identification Tags
- Pressure Sensitive Adhesive-backed Tags
- Merchandise Tags, Clothing, Jewelry and Hardware Display Tags
- Plastic and Non-Plastic Tags for Plants, Dogs/Animals and Labels
To learn more about Custom Tags and obtain a free sample or request a formal quotation, please complete our on-line form by clicking the "REQUEST INFORMATION” tab above.